5 Schritte für den sicheren Umgang mit Unsicherheiten in Ihrer Supply Chain
von Prof. Dr. Götz Andreas Kemmner
Bestände generieren Kosten, garantieren aber auch Sicherheit. Aber wie viel Sicherheitsbestand braucht Ihr Unternehmen eigentlich, um vor wirtschaftlichem Schaden abgesichert zu sein? Bei den meisten Unternehmen liegt von den falschen Artikeln der falsche Sicherheitsbestand an den falschen Stellen – von einem generellen Zuviel an Bestand ganz zu schweigen. Unsere fünf Schritte zum sicheren Umgang mit Unsicherheiten in Ihrer Supply Chain helfen Ihnen dabei, Ihren Sicherheitsbestand in den Griff zu bekommen und kontinuierlich daran zu arbeiten, Bestand und Kosten zu senken.
Wie viel Sicherheitsbestand versteckt sich in Ihren Lägern? Gegen welche Unsicherheiten möchten Sie sich rüsten? Wie viel Restrisiko bleibt bestehen? Diese einfachen drei Fragen verlangen präzise Antworten, besonders in der heutigen Zeit, in der wir zwar möglichst lieferbereit sein wollen, aber uns Überbestände nicht leisten können. Hätten Sie die Antworten parat? Vermutlich nicht. Sie könnten jetzt Ihren Logistikleiter fragen, Ihren Supply Chain Leiter, Ihre Disponenten oder Ihre Produktionsplaner. Wahrscheinlich könnten aber auch diese Ihre Fragen nicht beantworten. Dabei sind diese drei Fragen extrem wichtig. Sicherheitsbestände sind die Absicherung Ihres Unternehmens gegen wirtschaftliche Schäden wie Imageverlust, Umsatzeinbußen oder Profitausfall. Trotz dieser Vorteile ist der Sicherheitsbestand ein wichtiger Teil Ihres Gesamtbestandes und sollte daher präzise geplant sein.
Nach unserer Erfahrung sprechen drei Hauptgründe dafür, dass nicht nur der Supply Chain Manager, sondern auch die Führungsebene an sich mit dem Sicherheitsbestand und dessen Kosten vertraut sein sollte:
- Sicherheitsbestände fangen zwar alle großen Unsicherheiten ab, sollten aber nicht zu hoch sein.
- Das verbleibende statistische Restrisiko sollte bekannt sein.
- Der Sicherheitsbestand ist eine präzise statistische Kennzahl für die Abschätzung der Unsicherheiten in der Supply Chain des Unternehmens. Demzufolge sollte er regelmäßig erfasst und kontrolliert werden.
Aber was bedarf es den nun, um Ihre Sicherheitsbestände über die gesamte Supply Chain hinweg auf das richtige Niveau einzustellen? Die folgenden fünf Schritte helfen Ihnen auf Ihrem Weg zum Ziel:
5 Schritte zum professionellen Management Ihrer Sicherheitsbestände1. Überprüfen Sie Ihre derzeitige Strategie |
Schritt 1: Überprüfen Sie Ihre derzeitige Strategie
Beginnen Sie damit, dass Sie Ihr ERP-System einmal unter die Lupe nehmen. Praktisch jedes ERP-System ermöglicht die Bestimmung von Sicherheitsbeständen auf Material oder Artikel-Ebene. Wir werden später feststellen, dass diese Art des Sicherheitsbestands für spezielle Umstände gedacht ist und nicht als Absicherung gegen allgemeine Unsicherheiten. Bitten Sie Ihre IT einmal um eine Auflistung aller SKUs mit den benötigten sogenannten Grundbedarfen pro Artikel und den dazugehörenden ausgewiesenen Sicherheitsbeständen für alle Bestands- und Warenlager. Der Grundbedarf entspricht hierbei der Menge an Bestand, den Sie benötigen, um den durchschnittlichen Verbrauch eines Artikels während der Wiederbeschaffungszeit zu überbrücken. Bitten Sie um beide Zahlen in Mengen- und Werteinheiten.
Während die IT sich um diese Analyse kümmert, können Sie die verschiedenen Abteilungen auf ihre Sicherheitsbestände hin überprüfen. Das Streben nach Sicherheit ist ein menschlicher Reflex und betrifft jeden Aspekt unseres täglichen Lebens – so auch unsere Arbeit. Entsprechend hat natürlich auch jeder Mitarbeiter seine eigenen Tricks, um sich Sicherheitspuffer in seinen Teil der Supply Chain einzubauen. Vielleicht hat sich der Vertrieb die Sicherheitsbestände im ERP-System manuell eingestellt, genauso wie Disposition, Produktionsplanung und der Einkauf das getan haben könnten. Sicherheitsbestände können aber auch noch anderweitig versteckt liegen. Die Mindestbestellmengen oder die Produktionslosgrößen im ERP-System zu erhöhen sind andere beliebte Tricks, um Sicherheitsbestände zu verstecken. Zusätzlich zur Veränderung der Materialmengen werden aber auch gerne die Termine für Produktionsaufträge, Bestellungen oder Bedarfe einfach vorverlegt. Längere Eröffnungshorizonte sind übrigens auch sehr beliebt, sowie die „Anpassung“ von Sicherheitszeiten und zusätzlichen Auftragsbearbeitungs- oder Wareneingangsbearbeitungszeiten. Nicht vergessen werden dürfen die Vorräte „unter der Werkbank“, wo gerne weitere Artikel zur Sicherheit gelagert werden.
Aber, wenn sich jeder so sehr mit den Sicherheitsbeständen beschäftigt, warum sollte sich dann die Führungsriege den Kopf darüber zerbrechen? Nun, wären Sie ein General auf dem Schlachtfeld, würden Sie dann jeden Offizier und Soldaten mit der Bewaffnung herumlaufen lassen, die er für richtig hält? Ganz sicher nicht!
Sicherheitsbestände sind nur dann zuverlässig, wenn sie kontinuierlich sorgfältig identifiziert, überwacht und gepflegt werden. Alles andere ist nicht zuverlässig. Daher ist es absolut unerlässlich, dass bei dieser Überprüfung der Sicherheitsbestände alles auf den Tisch kommt. Schließlich geht es ja nicht darum, den Abteilungen ihre liebgewonnenen Sicherheitsbestände abzunehmen, sondern diese offen und zentral zu verwalten – alles in einer Waffenkammer, wenn Sie so wollen.
Haben Sie jetzt alle versteckten Sicherheitsbestände aufgespürt? Dann schauen wir uns einmal die folgende Grafik an:
Diese Kurve basiert auf vielen detaillierten Bestands-Simulationen. Sie zeigt, wie viel Sicherheitsbestand verschiedene Unternehmen für ihre angestrebte Lieferbereitschaft zusätzlich zu Ihren sogenannten Grundbedarfen im jeweiligen Lager benötigen.
Wie Sie sehen, benötigen manche Unternehmen nur wenig Sicherheitsbestand, während andere sehr viel mehr davon brauchen. Die Darstellung zeigt auch, dass 80% der Unternehmen mit 120% Sicherheitsbestand zusätzlich zum Grundbestand gegen Nachfrage-bezogenen Unsicherheiten abgesichert sind. Und genau das ist es, wofür die Sicherheitsbestände im ERP-System gedacht sind – und nur dafür: Eine Absicherung gegen Nachfrageschwankungen. Diese Zahl können Sie als ersten Hinweis abspeichern. Das bedeutet aber nicht, dass Sie jetzt 120% an Sicherheitsbestand für jeden einzelnen Artikel in Ihrem Lager aufbauen sollen. Für regelmäßig nachgefragte Artikel sollte ein wesentlich kleinerer Prozentsatz an Sicherheitsbestand ausreichen, während für sehr unregelmäßig nachgefragte Artikel diese 120% möglicherweise nicht ausreichen. Die 120% sind einfach der statistische Durchschnitt für den gesamten Sicherheitsbestand über alle Artikel in Relation zum Gesamt-Grundbedarf, der in 80% der Unternehmen ausreicht. Bei Ihnen liegt der erforderliche Prozentsatz evtl. deutlich geringer.
Inzwischen sollte Ihre IT Sie mit der Liste der artikel-spezifischen Sicherheitsbestände versorgt haben. Addieren Sie jetzt noch die versteckten Sicherheitsbestände aus Ihrer Bestandsaufnahme hinzu und vergleichen Sie diesen Gesamt-Sicherheitsbestandswert nun mit dem 120% KPI in der obigen Grafik. Das sollte Ihnen einen ersten Eindruck Ihrer tatsächlichen Lage in Sachen Sicherheitsbestand vermitteln.
Jede Lagerstufe in der Supply Chain hat eine Nachfrageseite (Lagerausgangsseite). Für Fertigwaren ist die Nachfrageseite der Markt, während Roh- und Einkaufsteile produktionsseitig nachgefragt werden. Um die hier auftretenden Bedarfsschwankungen abzufangen, ist auf diesen Bestandsebenen ein Sicherheitsbestand sinnvoll und nötig. Der benötigte Sicherheitsbestand, um mit diesen Bedarfsschwankungen umzugehen, sollte zum deutlichen Verständnis eigentlich als „Prognosesicherheitsbestand“ bezeichnet werden, wird aber allgemein nur „Sicherheitsbestand“ genannt. Das lässt allerdings außer Acht, dass es verschiedene Arten von Sicherheitsbeständen gibt, und das führt uns direkt zu Schritt 2:
Schritt 2: Identifizieren Sie die verschiedenen Unsicherheiten, gegen die Sie sich wappnen wollen
Sicherheitsbestände sollen Unsicherheiten abfangen. Aber welche Arten von Unsicherheiten sind das genau? Und welche davon lassen sich tatsächlich durch den Bestand beseitigen?
Ganz pragmatisch gesehen, besteht eine Supply Chain mit Beschaffung, Produktion und Distribution aus einem Netzwerk von Lagerstufen mit Zeitintervallen dazwischen, die für Transport, Produktion oder sonstige Zeitsegmente benötigt werden. Unsicherheiten in Ihrer Supply Chain stellen sich als Störungen auf der Versorgungsseite einer Lagerstufe, der Nachfrageseite einer Lagerstufe oder im Lager selbst dar. Soweit es die Materialwirtschaft betrifft, treten diese Störungen wie folgt auf:
- Auf der Versorgungsseite: Schwankungen der Lieferzeit, Abweichungen der Liefermengen oder Abweichungen in der Produktqualität,
- Auf der Nachfrageseite: Schwankungen der Nachfrage auf der Bedarfsseite oder
- Im Lager: veraltete Bestände, Bestandsdifferenzen, Teilebeschädigung oder Teileverlust (dieses Thema sei aber einem anderen Beitrag vorbehalten).
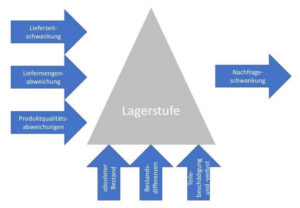
Das mag jetzt recht einfach klingen, aber was sind die Charakteristika eines unzuverlässigen Lieferanten? Schwankungen der Lieferzeit, Abweichungen der Liefermenge oder mangelnde Produktqualität. Was sind dagegen die Charakteristika einer unzuverlässigen Produktion bzw. eines inkonsistenten Herstellungsprozesses? Genau, Schwankungen der Lieferzeit, Abweichungen der Liefermenge oder mangelnde Produktqualität.
Unzuverlässige Transportwege aus dem Niemandsland, intransparente Zollabfertigungen in irgendeiner Bananenrepublik, verzögerte Wareneingangsprüfung, falsche Lieferung, Transportschäden – all das sind Faktoren, die zu Schwankungen der Lieferzeit, Abweichungen der Liefermenge oder mangelnder Produktqualität führen. Natürlich können Lieferungen auch zu früh und in zu großer Menge erfolgen, aber das hat wenigstens keinen negativen Einfluss auf die Lieferbereitschaft zum Markt hin.
Lassen Sie uns jetzt noch einen Blick auf die verschiedenen Lagerstufen einer Supply Chain werfen. Um die hier benötigten individuellen Sicherheitsbestände festzulegen, müssen wir die Schwankungen der Lieferzeit, Abweichungen der Liefermenge, mangelnde Produktqualität und Nachfrageschwankungen über alle Lagerorte hinweg quantifizieren.
Sie werden mir sicherlich zustimmen, dass das Fertigwarenlager oder das Komponentenlager im Falle der kundenauftragsbezogenen Fertigung ihren Sicherheitsbestand auf jeden Fall benötigen, um gegen plötzliche Mehrbedarfe abgesichert zu sein. Sie könnten jetzt aber anmerken, dass es nicht in Ihrer Verantwortung liegen könne, sich gegen die Nachlässigkeit Ihrer Lieferanten abzusichern, aber machen Sie sich bitte klar: Das tun Sie heute schon, und das noch mit beträchtlichem finanziellen Aufwand!
Ihre Einkäufer reisen um die halbe Welt auf der Suche nach alternativen Lieferquellen; Ihre Disponenten verbringen Stunden am Telefon, um auf Lieferantenseite mehr Teile oder schnellere Lieferungen auszuhandeln; Ihr Vertrieb beschwichtigt Ihre Kundschaft, die dringend auf die bestellte Ware wartet; Ihre Qualitätssicherung muss schon wieder einen Abweichungsbericht erstellen, damit Ihre Produktion zumindest die eiligsten Aufträge fertigstellen kann.
Selbstverständlich müssen Sie sich damit befassen, wie Sie diese Sicherheitsbestände durch entsprechende Maßnahmen in den Griff bekommen, und das ist Kern des Arbeitsschrittes 4. Es kann aber manchmal kostengünstiger sein, die Lawine an Problemen zuerst einmal dadurch aufzuhalten, dass man im Einkaufswarenlager genug Sicherheitsbestände aufbaut und so verhindert, dass sie durch die gesamte Supply Chain bis zu Ihren Kunden hindurchfegt. Daher berechnen wir im nächsten Schritt die benötigten Sicherheitsbestände und schauen, ob sich die erhöhten Bestände bezahlt machen.
Schritt 3: Die individuell benötigten Sicherheitsbestandshöhen bestimmen
Für diesen Schritt brauchen Sie ein wenig Kenntnis in Statistik und Wahrscheinlichkeitsrechnung. Falls Sie nicht wirklich Freude an Statistik haben, wie es Ihre Kollegen im Qualitätsmanagement hoffentlich tun, sollten Sie jetzt vielleicht einen Experten zu Rate ziehen.
Die korrekte Berechnung der Sicherheitsbestände ist keine einfache Sache. Und sie benötigt leider etwas mehr Einsicht in die Materie als die bloße Anwendung einer mathematischen Formel. Eine ausführliche Erklärung würde Sie vermutlich eher langweilen, daher an dieser Stelle nur ein paar Hinweise. Schauen wir zunächst einmal auf die Sicherheitsbestände der Nachfrageseite. Hier führen gewöhnlich drei Fehler zu falschen Sicherheitsbestandsniveaus und zusätzlich zu falschen Bedarfsprognosen:
Prognosefehler 1: | Prognosen und Sicherheitsbestände werden überwiegend mit Blick auf vorherige Verbräuche erstellt. Wenn Sie nicht sicherstellen, dass Ihr ERP-System die korrekte Bedarfszeitreihe für seine Kalkulationen heranzieht, erhalten Sie trotz perfekter Berechnung nur perfekten Müll. |
Prognosefehler 2: | Es gibt einen statistischen Zusammenhang zwischen Bedarfsprognose, Sicherheitsbestand und Soll-Lieferbereitschaft. Viele ERP-Systeme auf dem Markt ignorieren diesen Zusammenhang oder ermöglichen die Berechnung statistischer Sicherheitsbestände erst gar nicht. |
Prognosefehler 3: | ERP-Systeme berechnen Prognosen und Sicherheitsbestände für 90% der Artikel meistens falsch, da sie statistisch unzureichende Methoden anwenden. Diese Methoden gehen von einer normalverteilten Bedarfskurve aus, was aber auf den Großteil der Artikel nicht zutrifft. |
Um verlässliche Sicherheitsbestände zu berechnen, sind verteilungsfreie Verfahren oder ein spezieller Simulationsansatz zur Erstellung von Prognosen und Ermittlung von Sicherheitsbeständen unerlässlich.
Sicherheitsbestände, die Unsicherheiten auf der Wareneingangsseite abfangen, nennt man Liefer- oder Versorgungssicherheitsbestände. ERP-Systeme kümmern sich gewöhnlich nicht um diese Sicherheitsbestände. So werden die bestehenden Unsicherheiten auf der Wareneingangsseite des Lagers meistens durch die Verlängerung der Wiederbeschaffungszeit gepuffert und somit Schätzwerte in die Bedarfsplanung eingebracht. Die Verlängerung der Wiederbeschaffungszeit birgt indes ein Gefahrenpotenzial, besonders bei der Eigenfertigung. Allzu oft beginnt hier der Fehlerkreis der Fertigungssteuerung, der in abnehmender Lieferbereitschaft und erhöhten Umlaufbeständen endet.
Hier können Experten ebenfalls hilfreich sein, auch wenn Sie das vielleicht nicht hören möchten. Sehen Sie es einmal so: Selbst wenn Sie ein hervorragender Autofahrer sind, schrauben Sie nicht selbst am Motor Ihres Gefährts herum, sondern überlassen die komplexe Abstimmung von Zündung, Verbrennung und Ventileinstellung lieber einem Experten. Die Supply Chain Ihres Unternehmens „fahren“, d.h. sie planen und kontrollieren zu können, ist ein anderes Paar Schuhe als die nötigen Planungs- und Kontrollprozesse zu erstellen, einzuführen und abzustimmen.
Sicherheitsbestände können viel Liquidität binden und daher viel Geld kosten. Wie bereits gezeigt, können allein die Sicherheitsbestände für Bedarfsschwankungen 120% oder mehr Ihres Grundbestands betragen.
Aus diesem Grund sollten Sie die Anpassung Ihrer Sicherheitsbestände an einen Prozess zur Bestandsoptimierung koppeln. Nach unserer Erfahrung können 80% unserer Kunden ihren Gesamtbestand um 20% verringern, wenn die Sicherheitsbestände korrekt festgelegt und die Bestände optimiert werden. Das kompensiert die höheren Sicherheitsbestände sowie die wahrscheinlich anfallenden Beratungskosten und lässt Ihnen dabei noch einiges an liquiden Mitteln zur Verfügung. Zudem sparen Sie jährlich Lagerhaltungskosten ein.
Da Sie mittlerweile die nötigen Sicherheitsbestände ermittelt haben dürften, können wir nun fortfahren.
Schritt 4: Bauen Sie die nötigen Sicherheitsbestände auf und eliminieren Sie gleichzeitig die Bestandstreiber
Der erste Teil mag jetzt, da Sie die benötigten Sicherheitsbestände ermittelt haben, trivial wirken, aber die Bereitstellung von zusätzlich benötigtem Material oder Teilen kann sich als schwierig erweisen. Wenn Sie in Zeiten des Überflusses keine Sicherheitsbestände aufbauen, werden Sie sie in Zeiten der Not nicht zur Hand haben. Weil es so schwierig ist, Sicherheitsbestände aufzubauen sollten Sie sofort damit beginnen, auch wenn das langfristige Ziel in der Reduktion oder Vermeidung derselben besteht. Daher sollten Sie sich beim Aufbau des benötigten Sicherheitsbestands schon mit dessen Vermeidung beschäftigen und folgende Fragen beantworten:
- Welche Grundursachen stecken hinter den Lieferzeitschwankungen, Mengenabweichungen oder Qualitätsmängeln der Lieferung auf Wareneingangsseite?
- Wer ist für diese Sicherheitsbestandstreiber und deren Beseitigung verantwortlich?
- Welche dieser Ursachen (Sicherheitsbestandstreiber) können kurzfristig eliminiert werden?
- Welche der verbleibenden Ursachen treten so regelmäßig auf, dass Sie einen adäquaten Sicherheitsbestand dauerhaft halten sollten?
- Ist es möglich die Wiederbeschaffungszeit eines Artikel in einer Bestandsstufe zu reduzieren? Kürzere Durchlaufzeiten benötigen weniger Sicherheitsbestand!
- Gibt es eine Abteilung, die für die verbleibenden Sicherheitsbestände aufkommen muss?
Um ein Problem zu lösen, müssen dessen Ursachen identifiziert werden und die verantwortliche Abteilung, die über Ansatzpunkte zur Beseitigung des Problems verfügt, muss bei der Lösung helfen. Eine Abteilung, die ein durch sie verursachtes Problem nicht lösen kann, sollte für die daraus verursachten Kosten in der Betriebsabrechnung belastet werden – aber das ist vielleicht nur Träumerei.
In der Praxis ist es häufig ein wenig komplizierter und die verantwortliche Partei kann nicht direkt ermittelt werden. In diesem Falle sollte die Abteilung, die am nächsten an der Ursache dran ist, die Verantwortung übernehmen.
Schauen wir uns einmal die ‘üblichen Verdächtigen’ an:
Auf Nachfrageseite sind schlechte statistische Prognosen und fehlerhafte Sicherheitsbestandsberechnungen sowie ungenügend vorhersagbares Verhalten von Kunden und Märkten der Grund für Über-(Sicherheits-)Bestände. Für Ersteres müsste sich eigentlich das Supply Chain Management die Kappe aufziehen, während Letzteres zumindest annähernd in der Verantwortung des Vertriebs liegt. Können die Kunden eventuell dazu motiviert (oder erzogen) werden, bessere Vorhersagen zu liefern oder rechtzeitig zu bestellen? Können Kunden, die sich als unverbesserliche Bestandstreiber herausstellen, auf vernünftige Weise dafür mit Kosten belegt werden? Auf lange Sicht gesehen tragen alle Parteien einer Supply Chan die Kosten gemeinsam. Schlaue Kunden sollten daher an einer verbesserten Prognose ernsthaft interessiert sein (ich weiß, wieder eine Träumerei meinerseits).
Nachlässige Pflege des Produktportfolios ist ein weiterer Auslöser für hohe Sicherheitsbestände. Unregelmäßig nachgefragte Produkte, die nur wenig am Umsatz ausmachen, werden als CZ-Artikel klassifiziert. In manchen Unternehmen machen sie zwischen 30% und 50% der gesamten SKU aus und erfordern unnötig hohe Sicherheitsbestände. Das Vertriebs-Team und das Produktmanagement könnten hier die Lieferbereitschaft reduzieren oder aber das Produktportfolio bereinigen. Die Kosten für den verbleibenden Sicherheitsbestand müssten über die jeweiligen Verkaufspreise gedeckt werden. Leider werden die Kosten aber proportional über alle Artikel im Verhältnis zu ihrem Umsatz (nach „Tragfähigkeit“) verteilt und meist nicht den Artikeln belastet, die diese Kosten verursachen. CZ-Artikel können daher falsche Deckungsbeiträge aufweisen und somit vorgaukeln, dass Sie daran verdienen. Bei exakterer Kostenzuordnung ist dies nach meiner Erfahrung oft nicht so.
Auf der Wareneingangsseite sollte der Einkauf dafür sorgen, dass Lieferanten verlässliche Lieferzeiten, Liefermengen und Produktqualität einhalten. Einkäufer, die sich allein darauf beschränken, die Einkaufspreise niedrig zu halten, anstatt die kompletten Betriebskosten im Zaum zu halten, tragen zu überschüssigen Sicherheitsbeständen bei und sollten daher dazu gedrängt werden, die Unzuverlässigkeit seitens der Lieferanten zu überwachen. Natürlich wird der Einkauf jetzt einwenden, dass einige Einkaufsteile hochentwickelt sind, nur von wenigen Anbietern zu erhalten oder in absurd großer Bandbreite zur Verfügung stehen müssen. Nun gut, dann müssen eben Entwicklung und Fertigung ebenfalls zur Verantwortung gezogen werden!
Befinden Sie sich auf der Beschaffungsseite der Supply Chain und müssen Bedarfsschwankungen an Ihre Lieferanten weitergeben oder aber Sicherheitsbestände aufbauen, versuchen Sie herauszufinden, wer genau in der Supply Chain diese Schwankungen verursacht: Kunden, Vertrieb oder Produktion? Die Wahrnehmung dieses Problems – und damit dessen Lösung – lässt sich leider nur so erreichen.
Und nun endlich zur Eigenfertigung. Terminverzögerungen, abweichende Liefermengen und Qualitätseinbußen gibt es auch hier. Aber man muss schon sehr genau hinschauen, um hier die Bereiche zu finden, die helfen können, die Situation zu verbessern. Bei der Eigenfertigung können Sicherheitsbestände aufgrund von Produktionsproblemen oder unzuverlässiger Fertigungssteuerung erforderlich werden. Wenn Fertigteile oder Wareneingänge nicht umgehend auf Qualität geprüft und freigegeben werden, hat das Qualitätsmanagement noch einiges an Hausaufgaben zu erledigen.
Eine klare Zuordnung der Verantwortung für Maßnahmen gegen die verschiedenen Sicherheitsbestandstreiber hilft beim letzten Schritt:
Schritt 5: Entwickeln Sie ein Sicherheitsbestandsmanagement und führen Sie einen kontinuierlichen Verbesserungsprozess ein
Wie wir hoffentlich verdeutlichen konnten, sind Sicherheitsbestände ein guter Indikator für Schwachstellen in Ihrer Supply Chain. Wegen Problemen im Produktionsprozess an zusätzlichen 50% der Gesamtbestandsmenge festhalten zu müssen, das tut weh. Genauso schmerzhaft ist es, die Notwendigkeit von Sicherheitsbeständen zu ignorieren. Wir haben nur zwei Ansätze, um mit diesen Unsicherheiten in unseren Supply Chains fertig zu werden: Entweder müssen wir diese Unsicherheiten reduzieren bzw. beseitigen oder wir kompensieren sie durch Sicherheitsbestände (oder Überkapazitäten, was wiederum Kosten verursacht). Sie werden vielleicht weder willens noch in der Lage sein, alle benötigten Sicherheitsbestände aufzubauen, um alle Unwägbarkeiten abzusichern, dennoch bringt eine Kalkulation des benötigten Sicherheitsbestandes diese versteckten Kosten erstmalig ans Licht und hilft dabei, Prioritäten zu setzen.
Und nun, bevor alle sich eiligst ans Werk begeben: Ein systematischer Ansatz könnte hilfreich sein. Daher schlage ich die folgenden Prozessschritte vor:
- Identifizieren Sie alle Unsicherheiten in Ihrer Supply Chain
- Quantifizieren Sie die benötigten Sicherheitsbestände
- Etablieren Sie die wichtigsten Sicherheitsbestände, um Ihre Supply Chain abzusichern
- Hinterfragen Sie die wahren Ursachen dieser Unsicherheiten
- Ordnen Sie die Verantwortung für die Verringerung der Unsicherheiten zu
- Entwickeln Sie Lösungen, um die Unsicherheiten zu reduzieren
- Initiieren Sie Maßnahmen
- Überwachen Sie die Ergebnisse
- Verbessern Sie kontinuierlich Ihre Lösungsansätze
Zum guten Schluss möchte ich nochmals auf eine Statistik zurückkommen:Die besten Unternehmen arbeiten mit Sicherheitsbeständen von weniger als 25% ihres Gesamtbestandes. Wir hoffen und glauben fest daran, dass unsere fünf Schritte Ihnen dabei helfen werden in diese Liga aufzusteigen und werden Sie gerne auf dieser Reise unterstützen.