Dispositionsparameteroptimierung ist heute eine in vielen Unternehmen diskutierte und angewendete Methodik. Eine konsequente Pflege der Dispositionsparameter nutzt aber nur dann etwas, wenn die tägliche Disposition sich auch weitgehend daran hält. Mit Hilfe des Zielbestandsmanagements lässt sich die Anwendung eines Disporegelwerks laufend wirkungsvoll überwachen und das Ziel hoher Lieferfähigkeit bei möglichst geringen Bestände bleibt im Fokus.
Unter der Optimierung von Dispositionsparametern versteht man die richtige artikelspezifische Festlegung von Planungs-, Steuerungs- und Dispositionsparametern und -verfahren sowie das laufende Nachjustieren dieser Parameter- und Verfahrenseinstellungen. Vereinfachend spricht man gerne von „Dispoparameteroptimierung“ oder „DPO“. Dieses Nachjustieren geschieht bei der DPO nicht, indem Artikel für Artikel von den Anwendern analysiert und Stammdatenanpassungen entsprechend ihrer Vorstellungen und Erfahrungen individuell durchgeführt werden. Der DPO liegt vielmehr ein Dispositionsregelwerk zugrunde. Dieses Regelwerk definiert, welche Stammdateneinstellungen bei welchen Artikeleigenschaften vorzunehmen sind.
Ein klassisches und einfaches Beispiel stellt die Lieferbereitschaft dar. Hierzu könnte in einem Disporegelwerk beispielsweise festgelegt werden, dass alle A-Artikel mit regelmäßiger Nachfrage, sogenannte AX-Artikel, immer mit einer Lieferbereitschaft von 98% gefahren werden, während stark unregelmäßig nachgefragte CZ-Artikel nur mit 93% disponiert werden sollen. Dadurch, dass man Stammdateneinstellungen nicht an eine Materialnummer, sondern an Materialeigenschaften hängt, lassen sich aus einem Disporegelwerk erforderliche Stammdatenveränderungen ablesen und diese können mit Unterstützung geeigneter Softwaretools effizient im ERP-System nachgepflegt werden.
Der große Vorteil dieser Disporegelwerke:
- Stammdateneinstellungen hängen an objektiven Regeln und nicht an subjektiven Meinungen der einzelnen Anwender.
- Mit geeigneten Werkzeugen können die Stammdateneinstellungen simulativ so optimiert werden, dass das ERP-System möglichst wirtschaftliche Dispositionsvorschläge generiert.
- Ein leistungsfähiges Disporegelwerk ermöglichst auch einem unerfahrenen Disponenten eine Disposition auf hohem Niveau.
- Der Dispositionsprozess lässt sich deutlich automatisieren und effizienter durchführen.
Es gibt nur wenige Einsatzfälle, in denen ein Dispositionsregelwerk praktisch zur vollautomatischen Disposition eingesetzt wird. Mit einem optimierten Disporegelwerk lässt sich aber auf jeden Fall ein Teil der Dispositionsarbeit, primär für regelmäßige Artikel einerseits, für unregelmäßige C-Artikel andererseits, automatisieren.
Letztlich kann aber auch das leistungsfähigste Dispositionsregelwerk nicht sicherstellen, dass bei allen Artikeln immer die richtigen Dispositionsvorschläge durch das ERP-System erarbeitet werden. Dispositionsregelwerke und ERP-Systeme können bei der Berechnung von Bestell- oder Fertigungsvorschlägen nur auf den Informationen aufsetzen, die im ERP-System abgebildet sind.
Viele Informationen, über die Fertigungssteuerer und Disponenten verfügen, sind im ERP-System gar nicht hinterlegt, z. B.:
- dass ein Lieferant vorübergehende Lieferschwierigkeiten hat,
- ein Alternativlieferant momentan besonders günstige Preise bietet,
- in der Fertigung eine Anlage ausgefallen ist,
- der Vertrieb mit einem wichtigen Kunden wegen eines kurzfristigen Großauftrags in Verhandlungen steht.
Diese und ähnlich geartete Informationen werden in den wenigsten ERP-Systemen detailliert hinterlegt und können beim Erstellen von Dispovorschlägen somit auch nicht berücksichtigt werden.
Erfahrungsgemäß darf man davon ausgehen, dass in Handelsunternehmen ca. 70-80% der Dispositionsvorschläge ohne erforderliche Anpassungen von Mengen oder Terminen durch die Anwender übernommen werden können. Bei Produktionsunternehmen dürfte die Rate etwa 10% geringer sein.
Ein gewisser Anteil an Dispositionsvorschlägen, aber eben nur ein gewisser Anteil, muss von den Anwendern hinsichtlich Mengen, Terminen, Lieferanten, Produktionsanlagen oder ähnlichem angepasst werden.
Um die Potenziale eines guten Dispositionsregelwerks nachhaltig in der Praxis umzusetzen, ist ein geeignetes Controlling erforderlich, mit dem erkannt werden kann, in welchem Maß die tatsächliche Disposition von den Dispositionseinstellungen des ERP-Systems laut Disporegelwerk abweicht . Als wirkungsvolles Controllinginstrument hat sich dabei ein sogenanntes Zielbestandsmanagement bewährt.
Kern des Zielbestandselements sind materialnummernspezifisch ermittelte Zieldurchschnittsbestände, der Einfachheit halber als „Zielbestände“ bezeichnet. Der Zielbestand eines Artikels ergibt sich aus den Dispositionseinstellungen des ERP- oder Warenwirtschaftssystemslaut Disporegelwerk.
Der Zielbestand lässt sich am einfachsten am Beispiel einer Meldebestandssteuerung verdeutlichen (Abb.1):
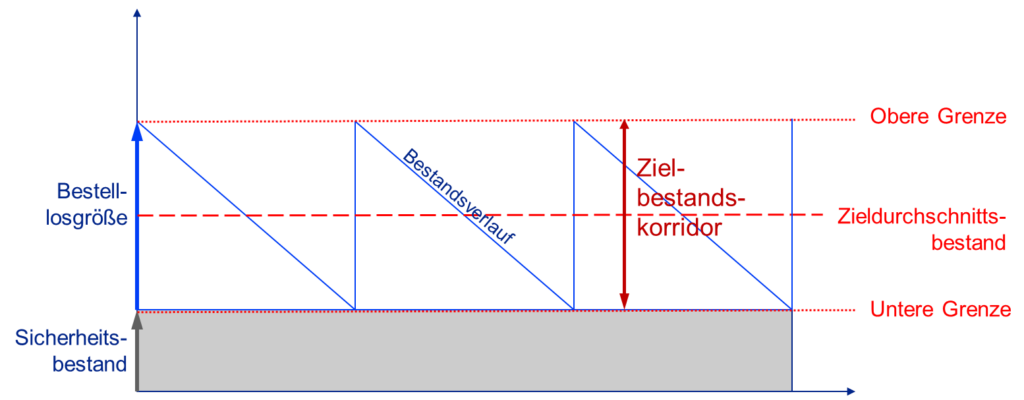
Bei den in Abb. 1 wiedergegebenen Dispositionseinstellungen zu Sicherheitsbestand und Bestelllosgröße ergibt sich der angezeigte Zieldurchschnittsbestand.
Nun verläuft der Bestand eines einzelnen Artikels nicht entlang seiner Zieldurchschnittsbestandslinie sondern folgt dem idealtypisch dargestellten Sägezahnverlauf. Bezogen auf eine einzelne betrachtete Materialnummer muss dies in Zielbestandsmanagement in Form eines Zielbestandskorridors berücksichtigt werden (Abb. 1). Wird ein Artikel entsprechend den Dispositionseinstellungen des ERP-Systems disponiert, dann sollte sich sein Bestandsverlauf im Zielbestandskorridor befinden. Störungen, wie kürzere oder längere Wiederbeschaffungszeiten, Teillieferungen, Anlagenausfälle oder ähnliches, können dazu führen, dass der Bestandsverlauf den Korridor verlässt.
Betrachtet man anstelle eines Artikels ein größere Gruppe von Artikeln, z.B. alle Artikel einer Warengruppe, eines Werkes oder einer Materialart, so neutralisieren sich die Schwankungen der Zielbestandsverläufe und man kann nach dem statistischen Gesetz der großen Zahlen davon ausgehen, dass die Summe der Bestände der einzelnen Artikel zu einem bestimmten Betrachtungszeitpunkt der Summe der Zielbestände entsprechen sollte, sofern sich alle Artikel in ihren Bestandskorridoren bewegen.
Eine Addition von Beständen oder Zielbeständen über eine Gruppe von Artikeln kann zumeist nicht auf Basis physischer Einheiten wie Stück, Tonnen, Beutel oder m² durchgeführt werden. Es macht wenig Sinn, fünf Haarnadeln zu 8 Laptops zu addieren; die Betrachtung der Summenwerte muss in Geldeinheiten erfolgen. An dem Beispiel der 5 Haarnadeln zu je 0,5 ct und den 8 Laptops zu je 560€ wird deutlich, dass bei dieser Betrachtung der Wert eines Artikel automatisch in die Zielbestandsbetrachtung einfließt. Wir der Zieldurchschnittsbestand der 5 Haarnadeln um 500% überschritten, liegen 5 x 2,5ct zu viel auf Lager. Wir der Zielbestand der Laptops um 12,5% überschritten, liegen 560€ zu viel auf Lager. Zielbestandsabweichungen teurer Artikel schlagen im Zielbestandsmanagement deutlicher durch als Abweichungen bei geringwertigen Artikeln, was gewollt ist.
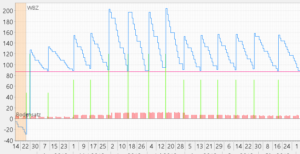
Beim Zielbestandscontrolling interessierten im Schwerpunkt nicht die Einzelartikel, für die es immer wieder Gründe gibt, warum sie aus dem Zielbestandskorridor ausbrechen, sondern die Zielbestands-Situation in den betrachteten Auswertungsgruppen (vgl. Abb. 2), z.B.:
- Wie groß ist der Anteil von Artikeln, die unterhalb des Bestandskorridors liegen?
- Wie groß der Anteil derjenigen Artikel, die darüber liegen?
- Ist dieses Verhältnis im Zeitverlauf besser geworden?
- Wie viele Materialnummer in Summe liegen unterhalb, im und über dem Bestandskorridor?
- Wie groß ist der absolute Wert an Überbestand bzw. an Unterbestand?
Bei der Betrachtung einzelner Artikel interessieren vor allem die TOP 10 der Artikel mit Überbestand und die TOP 10 mit Unterdeckung.
Das gesamte Zielbestandsmanagement steht und fällt mit der Berechnung der materialnummernspezifischen Zielbestände und Zielbestandskorridore. Idealtypische Betrachtungen zur Ermittlung des Zielbestandswertes, wie im vorausgehend angeführten Beispiel, unterschlagen, dass in praxi die Dispositionsvorschläge des ERP-Systems gelegentlich daneben liegen, sofern der Anwender nicht eingreift. Deutlich zuverlässigere Zielbestandswerte erhält man deshalb, indem man über einen Simulationsprozess ermittelt, wie sich die artikelspezifischen Dispositionseinstellungen und -parameter in der Vergangenheit gegenüber der tatsächlichen täglichen Bedarfssituation verhalten hätten. Daraus ergibt sich ein weit realistischerer Zielbestand. Typischerweise simuliert man dafür die letzten zwölf Vergangenheitsmonate durch. Auf diese Weise werden in dem ERP-Optimierungssystem DISKOVER SCO der SCT GmbH beispielsweise die Zieldurchschnittsbestände Materialnummer für Materialnummer simulativ ermittelt.
Erste artikelspezifische Referenzwerte für ein Zielbestandscontrolling lassen sich aber auch mit Hilfe von Grobformeln erstellen.
Wird beispielsweise im Fall der Meldebestandssteuerung mit einer Bestelllosgröße gearbeitet, die zwar größer als die Mindestlosgröße, aber kleiner als der Grundbedarf ist, stellt sich der idealtypische Bestandsverlauf wie in Abb. 3 gezeigt dar.
Der Zieldurchschnittsbestand ergibt sich in diesem Falle zu:
Zielbestand = Sicherheitsbestand + 0,5*Max(Mindestlosgröße; Bestelllosgröße).
Für ein sinnvolles Zielbestandsmanagement muss der anzusetzende Sicherheitsbestand vom ERP-System ermittelt und nicht manuell nach Gefühl und Erfahrung gesetzt werden, sonst sind der Bestandswillkür Tür und Tor geöffnet und das gesamte Zielbestandsmanagement macht keinen wirklichen Sinn mehr.
Die in die Zielbestandsermittlung einzusetzende „Bestelllosgröße“ entspricht nicht der tatsächlichen Größe einer Bestellung oder eines erstellten Fertigungsauftrags, sondern der Bestelllosgröße, wie sie sich aus den Losgrößeneinstellungen im ERP-System ergibt.
Ist die Bestelllosgröße nicht konstant, sondern variiert von Bestellung zu Bestellung, kann man dies in der Grobformel theoretisch noch damit berücksichtigen, dass man die durchschnittliche Bestelllosgröße einsetzt. Praktisch besteht zumeist jedoch das Hindernis, dass die schwankenden vom ERP-System vorgeschlagenen Losgrößen der Vergangenheit nicht mehr bekannt sind. Die schwankenden Losgrößen lassen sich so allenfalls durch eine Auswertung der Dispositionslisten aus den Bestellvorschlägen der Zukunft ermitteln.
Die für ein Zielbestandscontrolling erforderlichen Kennwerte Zielbestand sowie obere und untere Toleranzgrenze werden am besten monatlich zu einem festen Stichtag ermittelt. Wegen der vorausgehend beschriebenen Problematik, im Nachhinein nicht mehr die tatsächlich vom ERP-System vorgeschlagenen Bestelllosgrößen ermitteln zu können, ist im Einzelfall zu prüfen, ob die durchschnittliche Bestelllosgröße in jeweils monatlich im Voraus ermittelt werden sollte, während der damit zu vergleichende Ist-Bestandswert am Ende der Monatsperiode abgegriffen wird. Auch diese Auswertung ist noch mit Ungenauigkeiten verbunden, da sich die vom System vorgeschlagenen Bestelllosgrößen innerhalb der Monatsperiode bei den meisten Materialien noch mehrfach verändern.
Ist klar, wie der Zieldurchschnittsbestand zu berechnen ist, dann ist es einfach, die obere und die untere Toleranzgrenze zu definieren. Für die Berechnung der oberen Toleranzgrenze muss zum Sicherheitsbestand lediglich anstelle der 0,5 der volle Term addiert werden. Die untere Grenze des Zielbestandskorridors entspricht dem Sicherheitsbestand.
Näherungsformeln zum Zielbestandsmanagement
Obere Toleranzgrenze
= Sicherheitsbestand + Max(Mindestlosgröße; Bestelllosgröße)
Zielbestand
= Sicherheitsbestand + 0,5*Max(Mindestlosgröße; Bestelllosgröße)
Untere Toleranzgrenze
= Sicherheitsbestand
Ein weiterer Nachteil der beschriebenen Grobberechnung der Zielbestände besteht in der idealtypischen Annahme regelmäßige Verbräuche. In der Praxis weisen die meisten Artikel gerade keine regelmäßigen Verbräuche auf. Präziser und belastbarer ergibt sich der Zielbestand erst, wenn man ihn mittels Simulation aufgrund von Vergangenheitsbedarfen aber mit den aktuellen Parametereinstellungen des Artikels ermittelt.
Mit einem solchen Zielbestandscontrolling werden Sie zukünftig rationell und wirkungsvoll überwachen können, in welchem Maße die operative Disposition und Fertigungssteuerung sich an die Vorgaben aus ERP-System und Disporegelwerk halten. Verfolgen Sie die Abweichungen im Zeitverlauf, hinterfragen Sie die Ursachen der Abweichungen im Allgemeinen sowie des Anwachsens von Abweichungen im Speziellen. Hierdurch werden Sie nicht nur die Disziplin der operativen Disposition und Fertigungssteuerung verbessern, sondern auch die Qualität Ihres Disporegelwerks steigern.