Neues logistisches Geschäftsmodell beim Schaltanlagen- und Schaltgerätebauer Fritz Driescher GmbH & Co. KG – marktsynchroner Wertstrom und beruhigte Fertigung
von Stefan Bünger, Manfred Bürger1, Andreas Gillessen, Prof. Dr. Andreas Kemmner
Steigende Marktschwankungen und Variantenvielfalt sowie kürzere Lieferzeiten bei nicht verschiebbaren Auslieferungsterminen verursachten bei der Fritz Driescher GmbH & Co. KG in Wegberg hohe Mehrarbeit und Unruhe in Produktion und Endmontage. Hinzu kam ein großer manueller Steuerungsaufwand in der Disposition mitsamt den daraus resultierenden Effizienzverlusten. Zusammen mit den Experten von Abels & Kemmner konzipierte die Geschäftsleitung das logistische Geschäftsmodell neu und baute eine marktsynchrone Wertschöpfungskette von der Komponentenfertigung bis zur Endmontage auf. Dadurch konnten die Produktion enorm beruhigt, Kapazitätsengpässe aufgelöst, der Durchsatz gesteigert und die Durchlaufzeit verkürzt werden. Der Endmontage stehen heute sowohl Kanban-Artikel als auch auftragsbezogen gefertigte Komponenten mit einer sehr hohen Lieferbereitschaft zur Verfügung. Die Materialbereitstellung für die Endmontage durch das Zentrallager wurde durch die Einführung von „Supermarktregalen“ erheblich optimiert. In der Folge konnte DRIESCHER.WEGBERG trotz starkem Umsatzwachstum Bestände reduzieren.
Die Fritz Driescher GmbH & Co. KG in Wegberg ist ein mittelständisches Unternehmen und spezialisiert auf die Entwicklung und den Bau von Schaltanlagen und Schaltgeräten für die Energieversorgung. Zum Produktspektrum gehören u. a. Mittelspannungsschaltanlagen (SF6-gas- und luftisoliert), Mittelspannungsschalter (Freiluft und Innenraum), Transformatorstationen, Niederspannungsschaltanlagen sowie Hoch- und Niederspannungs-Sicherungseinsätze.
Die Fertigung ist durch eine sehr große Fertigungstiefe gekennzeichnet, wobei die auftragsbezogene Komponentenfertigung die für die Endmontage von Schaltanlagen und Schaltgeräten benötigten Komponenten liefert. Die Komponentenfertigung besteht dabei u. a. aus der zerspanenden Bearbeitung, dem Blechbearbeitungszentrum, dem Roboterschweißzentrum, der Pulverbeschichtungsanlage, der Kleinmontage und der Stützerfertigung (Zweitwerk). Aus den eigengefertigten Komponenten baut wiederum die Endmontage auftragsbezogen die Schaltanlagen und Schaltgeräte zusammen.
Ausgangssituation:
Um als einziges mittelständisches Unternehmen in seiner Branche am Markt bestehen zu können, ist für DRIESCHER.WEGBERG neben technisch und qualitativ hervorragenden Produkten eine hohe Flexibilität bei Kundenwünschen erforderlich – und dies bei extrem kurzen Lieferzeiten und hoher Termintreue. Obwohl die termingerechte Auslieferung der auftragsbezogen montierten Schaltanlagen und Schaltgeräte weitgehend eingehalten werden konnte (die Auslieferungstermine stehen fest und können nicht verschoben werden), wurde die Terminsituation in den letzten Jahren zunehmend kritischer. Liefertermine konnten nur mit großen Reibungsverlusten und großem Engagement aller Beteiligten gehalten werden. Das bisherige logistische Geschäftsmodell war in Form einer auftragsbezogenen Komponentenfertigung sowie einer auftragsbezogene Materialbereitstellung für die Endmontage gestaltet. Aufgrund der Marktschwankungen, der Erhöhung der Variantenvielfalt sowie kürzerer Lieferfristen stieß dieses logistische Geschäftsmodell nun an seine Grenze. Weiterhin musste das Auftragszentrum die fehlende detaillierte Kapazitätsplanung sowie eine teilweise Terminierung der Komponentenfertigungstermine in die Vergangenheit durch manuelle Priorisierungen kompensieren. Die Folge waren laufend benötigte Abstimmungen zwischen Komponentenfertigung, Zentrallager, Endmontage und Auftragszentrum; aufgrund der Komplexität der Produkte und der Vielfalt der Teile eine fast unmögliche Aufgabe.
In der Endmontage fehlten daher laufend Komponenten, was dort zur Zwischenlagerung von Teilen und nicht fertig montierbaren Anlagen führte. Die Komponentenfertigung, insbesondere die zerspanende Bearbeitung, kämpfte mit hohen Auftragsrückständen und langen Durchlaufzeiten. Dank großer Flexibilität der Arbeitszeitkonten in der Komponentenfertigung sowie des relativ hohen Anteils an gefertigten Standardteilen konnten die Liefertermine mit hohem Kostenaufwand und durch große Bestände trotzdem gerettet werden. Um weiterhin wirtschaftlich, schnell und termintreu fertigen, montieren und liefern zu können, war ein neues optimiertes logistisches Geschäftsmodell erforderlich, das DRIESCHER.WEGBERG darüber hinaus auch neue Wettbewerbsvorteile verschaffen sollte.
Gute Voraussetzungen für eine 80/20-Nivellierung
Vor der Konzeption und Umsetzung des optimierten logistischen Geschäftsmodells stand die detaillierte Analyse der Ist-Situation. Eine Portfolioanalyse der Einzelteile machte dabei deutlich, dass ein Großteil der Fertigungsauslastung (ca. 69 %) durch nur ca. 10 % der Teile erfolgt, die einigermaßen regelmäßig benötigt werden und damit gut für eine sogenannte Pull-Steuerung nach dem Supermarkt-Prinzip geeignet sind. Die restlichen ca. 90 % zu fertigender Teile belegten das restliche Drittel der Fertigungskapazität. Damit bot sich als Kernelement des neuen logistischen Geschäftsmodells eine 80/20-Nivellierung in der Fertigung an. Damit diese 80/20- Nivellierung reibungslos funktioniert, waren allerdings eine Reihe von Voraussetzungen zu überprüfen bzw. zu schaffen.
So musste beispielsweise sichergestellt werden, dass für die auftragsspezifischen Teile eine entsprechende Fertigungskapazität mittelfristig planerisch freigehalten wird, damit diese Teile möglichst ohne Warteschlange gefertigt werden können.
Weiterhin galt es zu prüfen,
- wie sich die XY- bzw. die Z-Artikel in den verschiedenen Fertigungsbereichen auf die verschiedenen Maschinen verteilen,
- wie gleichmäßig die Kapazitätsbelastung mit XY-Teilen einerseits und Z-Teilen andererseits im Zeitverlauf ist,
- ob die Materialströme teilweise gezielt physisch getrennt werden können, indem den Z-Teilen gesonderte Maschinen zugewiesen werden,
- ob eine Linienfertigung für verschiedene Materialnummern aufgebaut werden kann.
Wie die Ergebnisse der Analysen zeigten, waren die vorhandenen Kapazitäten in den verschiedenen Fertigungsbereichen im Zeitverlauf ausreichend, um sowohl die zu bevorratenden XY-Artikel als auch die auftragsbezogen zu fertigenden Z-Artikel termingerecht zu produzieren.
Eine Trennung der Materialströme zwischen XY- und Z-Artikeln oder auch eine Linienfertigung auf verschiedenen Materialnummern war nicht notwendig bzw. sinnvoll.
Volle Fertigungstrichter waren zu leeren
Eine Durchlaufzeitenanalyse in der Komponentenfertigung zeigte allerdings, dass trotz eines ausgeglichenen Zu- und Abflusses an Fertigungsauftragsstunden zu lange Auftragswarteschlangen vor den verschiedenen Kapazitätseinheiten in der Produktion bestanden, die hauptverantwortlich für die langen Durchlaufzeiten waren. Der Arbeitsvorrat betrug im Durchschnitt 21 Arbeitstage und führte zu großen Problemen bei der Termintreue in der Komponentenfertigung.
Um die Komponentenfertigung logistisch richtig zu positionieren und auf kurze Durchlaufzeiten und hohe Termintreue auszurichten, musste der Umlaufbestand in der Komponentenfertigung mit folgenden Direktmaßnahmen reduziert werden:
- Der Fertigungsumlaufbestand wurde auf die neue erforderliche Zielgröße reduziert, indem dieFertigungskapazitäten vorübergehend durch Zusatz- und Geisterschichten sowie Auswärtsverlagerung von Aufträgen organisatorisch erhöht wurden.
- Eine Personalkapazitätssteuerung wurde erarbeitet und installiert, die den kurzfristig erforderlichen Bedarf an Personalkapazität für die verschiedenen Teilbereiche der Komponentenfertigung aufzeigt. Mit diesem Instrument konnte und kann die Fertigungsleitung die Mitarbeiterkapazitäten entsprechend dem aktuellen Fertigungsbedarf verschieben und die Leiharbeitskapazitäten zeitlich und quantitativ genau disponieren
- Fertigungsaufträge wurden nur noch zeitgerecht und nicht mehr verfrüht eingelastet.
- Fertigungsaufträge wurden grund -sätzlich nicht mehr in die Vergangenheit zurückterminiert. Im Verlauf von sechs Monaten gelang es mit diesen Maßnahmen, die Fertigungsauftragsdurchlaufzeiten auf im Schnitt vier Tage zu senken.
Weiterhin wurden im Rahmen der Ist-Analyse die Planung und Steuerung in der Disposition mit dem Baan 5-System sowie die Arbeitsorganisation in der Endmontage und der Komponentenfertigung im Detail analysiert und datentechnisch ausgewertet.
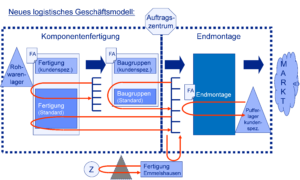
Neues Logistisches Geschäftsmodell:
Ist eine Fertigungssituation erst einmal so aus dem Ruder gelaufen, lässt sich die Situation nur dadurch wieder beheben, dass man die Produktionskette kapazitiv und auftragsseitig richtig ausbalanciert. Aufbauend auf den Ergebnissen der Ist- Analyse definierten und konzipierten die Berater das neue logistische Geschäftsmodell und die notwendigen Handlungsfelder. Ziel war es, das logistische Geschäftsmodell an die Marktanforderungen anzupassen und eine marktsynchrone Wertschöpfungskette aufzubauen.
Entsprechend sieht die Definition der mit dem neuen logistischen Geschäftsmodell verbundenen und umzusetzenden Handlungsfelder und Maßnahmenpakete aus:
- Endmontage:
- Zweibehälter-Kanban für XY- und einige Z-Teile in den Supermarktregalen der Endmontage.
- Komponentenfertigung:
- Durchlaufzeit Komponentenfertigung systematisch verringern,
- operatives Kapazitätsmanagement aufbauen,
- 80/20-Nivellierung der Fertigungskapazitäten für Standard (XY)- und auftragsspezifische (Z) Teile,
- Pull-Steuerung für einen Teil der Standard-Komponenten (XY-Teile),
- Push-Steuerung für die auftragsspezifischen Teile (Z-Teile).
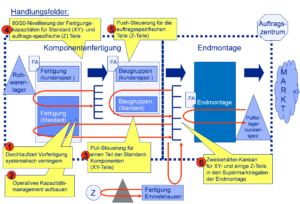
„Hasen“- und „Igel“-Strategie in der Komponentenfertigung:
Wie die Ist-Analysen untermauerten, eignete sich die Artikelstruktur hervorragend für eine 80/20-Nivellierung. Wurden bisher alle Artikel auftragsbezogen gefertigt und nur losgrößenbedingt gelagert, lagern die AB/XY-Artikel („Igel“-Artikel) nun unter dem neuen logistischen Geschäftsmodell über eine Pull- Steuerung (via Kanban) bestandsgeführt im Zentrallager bzw. in den Supermarktregalen der Endmontage. Der große Vorteil besteht in der jetzt kontinuierlicheren Auslastung der Kapazitäten.
Trotz dieser neuen Bestandsstufe für die AB/XY-Artikel konnten die Lagerbestände reduziert werden! Alle auftragsbezogen zu fertigenden Artikel können hierdurch priorisiert mit kurzen Durchlaufzeiten und schneller Verfügbarkeit („Hasen“- Artikel) gefertigt werden (Push- Fertigung via Fertigungsauftrag im Baan 5-System).
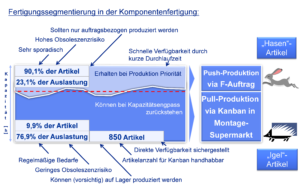
Pull-Steuerung via Kanban:
Für die sich regelmäßig verbrauchenden Artikel wurde eine Pull-Steuerung via Kanban aufgebaut. Hierzu musste im Baan 5-System eine entsprechende Erweiterung für die Kanban-Steuerung programmiert werden. Dies war auch für das Zweibehälter- Kanbansystem in der Endmontage notwendig.
Heute werden die Kanban-Karten der leergeworden Behälter der Komponentenfertigung im Zentrallager gescannt und der Gelbe und Rote Bereich der Kanbantafel elektronisch in Baan überwacht. Ist der Rote Bereich erreicht, muss die Komponentenfertigung die Produktion starten, ist der Gelbe Bereich erreicht, kann sie das tun. Über den Gelben Bereich wurde hiermit eine zusätzliche Flexibilität in der Komponentenfertigung geschaffen, um die Kapazitätsauslastung zu optimieren.
Operatives Kapazitätsmanagement:
Eine einfache Excel-Access-Applikation hilft zusätzlich, eine Kapazitätsplanung auf Basis der Baan 5-Daten für alle Fertigungskapazitäten aufzubauen. Kapazitätsbedarfe (Maschinen/Personal) werden jetzt ausgehend von den Fertigungsbedarfsterminen für jede Fertigungsstufe überwacht. Hierdurch sind aktuelle und zukünftige Engpasssituationen sofort sichtbar und können aktiv bearbeitet und damit in den meisten Fällen vermieden werden.
Zweibehälter-Kanban für XY- und einige Z-Teile in den Supermarktregalen der Endmontage:
Früher stellte das Zentrallager alle Komponenten für die auftragsbezogene Montage der Schaltanlagen und Schaltgeräte für die Endmontage bereit. Aufgrund der Vielzahl an benötigten Artikeln für eine Schaltanlage und der Probleme in der Komponentenfertigung hatte die Endmontage häufig mit fehlenden Komponenten zu kämpfen. In der Folge konnten die Mitarbeiter die teilmontierte Schaltanlagen nicht zu Ende bauen und mussten Komponenten zwischenlagern, was zu Platzproblemen und häufiger Materialsuche führte.
Unter dem neuen logistischen Geschäftsmodell lagern alle XY- und auch einige Z-Artikel in der Endmontage in einem Zweibehälter-Kanban- System. Dazu wurde die Endmontage so umgebaut, dass für jeden der acht Montagebereiche eigene Kanban- Regale und Palettenstellplätze entstehen konnten. Ist ein Behälter heute leer, wird über die Scannung des entsprechenden Barcodes ein Umlagerungsauftrag im Zentrallager generiert. Innerhalb von zwei Arbeitstagen muss der leere Behälter wieder aufgefüllt werden. Während dieser Umlagerungszeit bedienen sich die Mitarbeiter aus dem zweiten Kanbanbehälter mit den benötigten Komponenten. Dieses System ermöglicht es, die Endmontage mit einer Lieferbereitschaft von zum Teil über 98 % mit Standardkomponenten zu versorgen. Eine enorme Reduzierung der Auslagerungsvorgänge entlastete darüber hinaus insbesondere das Zentrallager. Dieses priorisiert bei den Umlagerungsvorgängen vom Zentrallager in die Endmontage jetzt, genauso wie die Komponentenfertigung, die auftragsbezogen gefertigten Komponenten, was wiederum zu einer hohen Verfügbarkeit aller Komponenten in der Endmontage geführt hat. In der Endmontage wurden für die acht Montagebereiche bisher insgesamt 3.176 Artikel auf das Zweibehälter-Kanbansystem umgestellt.
Um das Problem nicht zu Ende montierbarer Schaltanlagen und deren Zwischenlagerung mit anschließender Materialsuche zu vermeiden, wurde darüber hinaus im Baan 5- System die Materialbereitstellung (Kommissionier-Reports) für die auftragsbezogen gefertigten Artikel so reorganisiert, dass jetzt Umlagerungsaufträge in die Endmontage nur noch dann erfolgen, wenn eine 100-%-ige Materialverfügbarkeit aller Komponenten für einen Montageauftrag gegeben ist.
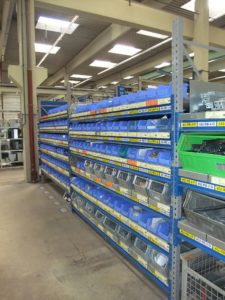
Regelwerk, Dispo-Parameter- Optimierung, Überwachung der Fertigungssegmentierung:
Um die Push- und Pull-Steuerung für die Komponentenfertigung und das Zweibehälter-Kanbansystem in der Endmontage effizient durchzuführen, justieren die Planer und Disponenten die Planungs-, Steuerungs- und Dispositions-Einstellungen im Baan- 5-System regelmäßig artikelspezifisch nach. Der „Betriebspunkt“ wird dabei immer so nachgeregelt, dass die Wertschöpfungskette kostenminimal funktioniert. Um dieses zu erreichen, galt es, ein Regelwerk für die Optimierung der Systemeinstellungen (Fachjargon: Dispo-Parameter- Optimierung) zu erarbeiten. Im Regelwerk erfolgte für die einzelnen Artikelklassen (ABC/XYZ/ELAN/etc.) die Definition der Parametereinstellungen wie Push-/Pull-Steuerung, Lieferbereitschaftsgrad, Sicherheitsbestand, Bestellmethode, etc.
Das gesamte Artikelspektrum, welches das Auftragszentrum betreut, strukturiert sich in
- Komponenten mit einigermaßen gleichmäßigen Bedarfen, und
- Komponenten mit geringem Wiederholungsgrad, sporadischem Bedarfsverhalten oder kundenspezifischen Teilen.
Während die erste Gruppe von Teilen via Kanban-Organisation gesteuert wird, wird die zweite Gruppe auch weiterhin konventionell gesteuert, um unnötige Bestände zu vermeiden und trotzdem die Liefertermine einzuhalten und Lieferzeiten weiter zu verkürzen. Die Anwendung des Regelwerks auf alle Artikel sowie die Ermittlung der zu ändernden Parametereinstellung im Baan-5-System kann nicht mehr von Hand erfolgen. Der dafür erforderliche Aufwand wäre viel zu groß. Aufgrund der Vielfalt der zu verändernden Systemeinstellungen, erfolgt dies jetzt mit Hilfe der Simulationssoftware DISKOVER SCO, die auch schon bei der Analyse der Ist- Situation und der Simulation verschiedener Szenarien zum Einsatz gekommen ist.
Mit Hilfe von DISKOVER SCO können Planer und Disponenten zusätzlich zur Dispo-Parameter-Optimierung drei weitere wichtige Aufgaben ebenfalls regelmäßig, effizient und halbautomatisch durchführen:
- die Überprüfung der Push-/Pull- Artikel für die Komponentenfertigung als auch für die Zweibehälter- Kanbanartikel der Supermarktregale in der Endmontage.
Welche Artikel aus dem Kanban- System herausgenommen und welche auf Kanban umgestellt werden müssen, wird von DISKOVER ermittelt und in Form eines Berichtes bereitgestellt. Diese regelmäßige Pflege ist notwendig, damit auch zukünftig die richtigen Teile im Kanban-System und die richtigen Teile im Push- System gesteuert werden. Ohne diese Pflege würde das gesamte Produktionssystem mittelfristig aus dem Gleichgewicht geraten. - das Nachjustieren der 80/20 Nivellierung.
Um die 80/20-Nivellierung im Gleichgewicht zu halten, ermittelt DISKOVER wie viel Produktionskapazität kalkulatorisch für die kundenspezifischen Push-Aufträge bereitgehalten werden muss und welche Kapazitäten im Schnitt für die Kanban-Fertigung verwenden werden können. Abhängig von der verfügbaren Kanban- Kapazität erfolgt sodann - das Nachdimensionieren der Kanban-Artikel.
Hierbei wird ermittelt und simulativ überprüft, wie groß die artikelspezifischen Umlaufbestände und damit die Anzahl der Kanban -Karten je Kanban-Artikel sein müssen. Zu viele Karten bedingen unnötige Bestände, zu wenig Karten führen zu Lieferbereitschaftsproblemen.
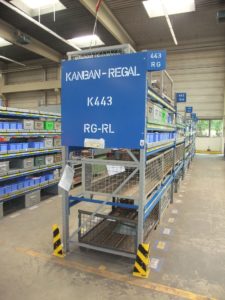
Praxisbewährung:
Das neue logistische Geschäftsmodell und der marktsynchrone Wertstrom haben bei DRIESCHER.WEGBERG zu einer großen Beruhigung in der Komponentenfertigung, dem Zentrallager und der Endmontage geführt. Die hohe Lieferbereitschaft in der Endmontage, die große Termintreue und die Steigerung des Durchsatzes in der Komponentenfertigung – ohne Kapazitätserweiterung – sowie die hohe Akzeptanz und Zufriedenheit der Mitarbeiter zeugen davon.
Die kanban-gesteuerten Artikel sind zu sogenannten Selbstläufern geworden, die lediglich in regelmäßigen Abständen überprüft und nachjustiert werden müssen; Auftragszentrum, Produktion, Zentrallager und Endmontage können sich auf die auftragsbezogen zu fertigenden Komponenten konzentrieren.
Mit der Umsetzung des neuen logistischen Geschäftsmodells hat DRIESCHER.WEGBERG seine Wettbewerbsposition am Markt deutlich gestärkt was sich im überproportional wachsenden Auftragseingang eindrucksvoll bemerkbar macht.
1 Stefan Bünger ist Prokurist und Manfred Bürger ist Leiter des Auftragszentrums der Fritz Driescher GmbH & Co. KG, Wegberg.
Weitere Informationen zu diesem Themenfeld finden Sie hier:
- Fertigungssegmentierung, Materialflussoptimierung und Heijunka-Steuerung in der Goldfedermanufaktur
- Anhaltender Aufschwung erschwert den Planungs- und Dispositionsprozess
- Supply Chain Optimierung für Retailer