Mit Formeln aus der Theorie zum Kostenoptimum in der Praxis?
Götz-Andreas Kemmner
Losgrößenverfahren zur Gesamtkostenreduktion von Lagerhaltung und Beschaffung erscheinen auf den ersten Blick sehr interessant. Um die Potenziale jedoch umfassend ausschöpfen zu können, müssen Anwender auch die Grenzen der Losgrößenverfahren kennen und sich bewusst sein, dass man mit ihnen nicht alle gesamtbetrieblichen Interdependenzen berücksichtigen kann. Für den punktgenauen Einsatz an der strategisch richtigen Stelle ist deshalb entsprechende Methodenkompetenz über die gesamte Supply Chain hinweg gefragt.
Über kaum ein Thema wurden und werden immer noch so viele Dissertationen geschrieben,wie über die Losgrößenoptimierung. Das zumindest zeigt, dass die Optimierung von Losgrößen in der Theorie noch nicht ausreichend gelöst zu sein scheint. Auch in der Praxis wird das Thema heiß diskutiert, denn damit die Losgrößen-Rezepte hier aufgehen, muss man genau verstehen, wie sie funktionieren und wo ihre Schwachpunkte liegen.
Ziele der Losgrößenverfahren
Durch das Losgrößenverfahren soll ein Optimum zwischen Lagerhaltungskosten auf der einen und Beschaffungskosten für die Eigenfertigung oder die Fremdbeschaffung auf der anderen Seite berechnet werden, um so die Gesamtkosten in einem vergleichsweise kleinen Segment einer ganzheitlichen Supply Chain zu minimieren. Das Problem dabei: Eine einzelne Losgrößenentscheidung, beispielsweise im Einkauf oder für einen spezifischen Wertschöpfungsschritt in der Produktion, muss nicht zwangsläufig für das Gesamtoptimum der Supply Chain förderlich sein. Hierum geht es aber letztlich.
Es geht zwar nur um die Kostenreduktion für ein Gut, doch Interdependenzen zwischen einzelnen Gütern müssen vorab spezifiziert werden. Erst dann kann man sich mit den optimalen Losgrößenverfahren beschäftigen. Fangen Sie also niemals ein Losgrößenprojekt an,ohne vorher auch einen Blick auf die gesamte Supply Chain geworfen zu haben. Die Grundlage aller Losgrößen-Berechnungen bildet dabei konsequenterweise die Ermittlung der relevanten Kosten.
Update 2021 : für aktuelleren Beitrag diesem Link folgen
Kostenarten bei der Losgrößenoptimierung
Allgemein sind dabei zwei gegenläufig reagierende Kostenarten zu betrachten: die Lagerhaltungskosten und die Beschaffungskosten. Die Lagerhaltungskosten setzen sich aus einer ganzen Reihe von Kostenarten zusammen. Neben den Zinsen des gebundenen Kapitals gehören hierzu auch weitere Kostenarten, die oft noch deutlich größer ausfallen. Das sind vor allem: Kosten für Alterung und Verschleiß, Verlust und Bruch, Transport und Handling innerhalb des Lagers, Lagerung und Abschreibung sowie Lagerverwaltung und Versicherung.
Zu den Beschaffungskosten der Eigen- oder Fremdfertigung zählen vor allem Bestellkosten, Rabatte, Boni, Skonti, Zusatzkosten bei ungünstigen Bestell- oder Fertigungsmengen, Transport-, Versicherungs- und Verpackungskosten, Auftragsbearbeitungskosten und natürlich die Rüstkosten.
Größere Losgrößen in der Beschaffung oder der Fertigung führen zu höheren Beständen und damit höheren Lagerhaltungskosten. Diese steigen im Allgemeinen proportional zur Losgröße, während die Beschaffungskosten degressiv fallen. Ein einfaches Beispiel: Fallen für ein bestelltes Teil dieselben absoluten Transportkosten an, wie für zwei Teile, dann trägt bei zwei bestellten Teilen jedes nur noch die Hälfte der Transportkosten (vgl. Bild 1). Um diese unterschiedlichen Kostenkurven zu einem Gesamtoptimum zu bringen, wurden und werden unterschiedliche Verfahren entwickelt, die man in der Summe unter Losgrößenverfahren zusammenfasst. Die Anwendung bedarf einerseits Methodenkompetenz innerhalb dieser Disziplin, wichtig ist aber auch der Blick auf das unternehmerische Ganze.
Die wichtigsten Losgrößenverfahren
Bei den Losgrößenverfahren unterscheidet man gewöhnlich zwischen statischen Verfahren und dynamischen Verfahren. Statische Verfahren (Andler-Verfahren) betrachten keine in der zeitlichen Abfolge variierenden Fertigungs- oder Bestellbedarfe, sondern nur die gesamte Bedarfsmenge innerhalb eines Betrachtungszeitraums und sind damit nur überschlägige Berechnungsverfahren.
Dynamische Verfahren bzw. periodische Losgrößenverfahren betrachten hingehen über einen Zeitraum hinweg z.B. den variierenden Bedarf pro Woche. Darüber hinaus berechnen sie Losgrößen pro Woche und rollierend. Sie sind damit grundsätzlich nachfrageorientierter und können sich so veränderten Bedarfen anpassen. Zu dieser Gruppe von Verfahren gehören:
- das Wagner-Whitin-Verfahren
- das Part-Period-Verfahren (Stück-Perioden-Ausgleichsverfahren)
- das Stückkosten-Verfahren (Verfahren der gleitenden wirtschaftlichen Losgröße)
- das Groff-Verfahren
- das Silver-Meal-Verfahren.
Die Menge unterschiedlicher Verfahren erklärt sich daraus, dass bisher niemand in einer Formel die komplexe Realität wirklich exakt abbilden konnte. Insofern stellen alle Losgrößenverfahren nur Näherungslösungen dar. Einige sind jedoch näher am Optimum als andere. Die oben aufgeführten Verfahren muss man deshalb sehr genau verstehen, um sie nutzbringend anwenden zu können.
Alle oben genannten Verfahren beschreiben das Zusammen- bzw. Gegeneinanderwirken von Lagerhaltungskosten und Beschaffungskosten in einer einstufigen Einprodukt-Fertigung ohne Kapazitätsbegrenzung. Ein Beispiel: Sie besitzen eine Druckmaschine, auf der Sie eine Druckplatte aufgespannt haben. Das Einrichten der Druckmaschine kostet Sie unabhängig von Ihrer Arbeitskraft Papier und Druckfarbe, da Sie eine ganze Zeit lang Makulatur produzieren, bis Sie die Maschine richtig eingerichtet haben. Da Sie dasselbe Dokument immer wieder produzieren müssen, stellt sich für Sie einzig und alleine das Dilemma aus hohen Fertigungslosen und damit geringen anteiligen Rüstkosten einerseits und hohen Lagerbeständen und Bestandskosten andererseits. Die Losgrößenberechnungsformeln der klassischen Verfahren versuchen genau für diese Situation eine “Trade-off”-Formel zu beschreiben.
Eigentlich tritt die Frage nach einer Losgröße jedoch erst auf, wenn mehr als ein Produkt gefertigt wird. Auch wenn mehrere Produkte auf einer Anlage gefertigt werden, stimmen unsere Formeln, sofern sich die Losgrößen der beiden Produkte nicht gegenseitig durch eine begrenzte Maschinenkapazität beeinflussen. Das ist in der jedoch häufig der Fall.
Der Einkauf muss auch übergeordnet optimieren
In der Beschaffung sieht es ähnlich aus. Auch hier kann häufig keine isolierte Losgrößenbetrachtung bei einem einzelnen Produkt angestellt werden. Zum einen können sich mehrere verschiedene Produkte Beschaffungskosten “teilen”: Denken Sie beispielsweise an einen LKW, der mit mehreren Produkten beladen werden kann. Zum anderen geht es häufig darum, den LKW voll zu bekommen, um möglichst geringe Transportkosten zu erreichen. Mehrere Produkte werden also gezielt zusammen bestellt und beeinflussen sich somit hinsichtlich ihrer Bestellmengen gegenseitig. Mit der vermeintlich “optimalen” Bestellmenge eines Produktes schränke ich folglich den Spielraum der Bestellmengen für die anderen Produkte automatisch ein.
Werfen wir nochmals einen Blick in die Produktion: In einer Fertigung, in der ich von Fertigungsstufe zu Fertigungsstufe die Losgrößen optimiere, arbeite ich beim Drehen mit 450 Stück im Fertigungsauftrag. Beim anschließenden Fräsen habe ich 380 Stück als “optimal” ermittelt und beim anschließenden Galvanisieren komme ich zu einer Losgröße von 1250 Stück. Die Folge: Zwischenbeständen, die bei der Einzelfall-Berechnung nicht berücksichtigt worden sind, und evtl. mehrere „optimale” Fertigungsmengen direkt nacheinander produziert werden müssen. Sie sehen, so einfach eine Formel im Einzelfall ist, so komplex ist die Realität.
Komplexer ist exakter, aber auch schwieriger
Dabei gibt es durchaus Losgrößenoptimierungsverfahren, die eine gesamte Prozesskette berücksichtigen. Will man nun aber realistischerweise auch noch berücksichtigen, dass die Kapazitäten auf den einzelnen Fertigungsstufen begrenzt sind, lässt sich die Realität nicht mehr vollständig mit all den gegebenen Interdependenzen und Limitierungen durchrechnen.
Lassen Sie uns noch einmal, anhand eines kleinen historischen Abrisses, einen kurzen Blick auf einige Formeln werfen, um sie konkret zu bewerten.

Andler ist oft zu simpel
Kurt Andler entwickelte 1929 eine Formel zur Berechnung einer wirtschaftlichen Losgröße. Die Andlerformel ermittelt das Minimum der Gesamtkostenkurve in Bild 1. Bei der Berechnung der Losgröße ging Andler davon aus, dass die Gesamtbedarfsmenge eines Artikels in einem Planungszeitraum,z.B. ein Jahr, bekannt ist. Die Formel leitet nun aus Lagerhaltungskosten einerseits und Beschaffungskosten andererseits die Losgröße ab, mit der immer wieder bestellt werden sollte. Da die Losgröße über den Planungszeitraum konstant bleibt, spricht man auch von einer statischen Losgrößenformel.
In der Praxis jedoch, sind Produktions- oder Bestellbedarfe über einen Planungszeitraum, typischerweise kürzer als ein Jahr, nicht konstant. Sie folgen vielmehr unregelmäßig aufeinander und fallen unterschiedlich hoch aus (Bild 2).
Folglich muss es in diesen Fällen eine genauere Lösung für eine wirtschaftliche Losgröße. Die entscheidende Antwort gaben zwei Amerikaner bereits 1958.
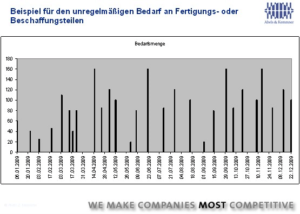
Wagner-Within ist sehr exakt
Die Herren Wagner und Whitin entwickelten ein Losgrößenberechnungsverfahren, mit dem dynamische Losgrößen berechnet werden konnten. Diese mathematische Lösung berücksichtigt, dass mit der Entscheidung über eine erste Losgröße im Betrachtungszeitraum automatisch auch der Spielraum für die Gestaltung der zeitlich nachfolgenden Losgrößen eingeschränkt wird. Das Wagner-Whitin-Verfahren ermittelt eine Folge von Losen mit unterschiedlicher Größe und unterschiedlichen Zeitabständen, welche die Gesamtkosten minimiert. Das Ergebnis ist eine wissenschaftlich präzise Antwort auf die Frage der richtigen Losgrößen bei einer einstufigen Einprodukt-Fertigung ohne Kapazitätsbegrenzung. Das Wagner-WhitinVerfahren lässt sich sogar mit der Hand rechnen, wird für Losgrößen für unzählige Produkte allerdings sehr komplex, auch für damalige Rechenmaschinen. Näherungsverfahren mit einfacheren Rechenmethoden mussten deshalb her, mit denen Computer, auf Kosten der Genauigkeit, zurechtkamen. So wurde beispielsweise 1968 das Part Period-Verfahren entwickelt, 1969 das nach seinen Entwicklern genannte Silver-Meal-Verfahren und 1979 das Groff-Verfahren.
Da diese Näherungsverfahren verschiedene Vereinfachungen vornehmen, ermitteln sie das Kostenoptimum auch bei unterschiedlichen Losgrößen. Die Abweichungen vom exakt rechnenden Wagner-Whitin-Verfahren können dabei sehr deutlich ausfallen, wie Bild 3 zeigt. Die heuristischen Verfahren zur Losgrößenoptimierung liegen teilweise weit von exakten Ergebnis des Wagner-Whitin-Verfahrens weg, wie das Beispiel einer Bedarfszeitreihe zeigt.
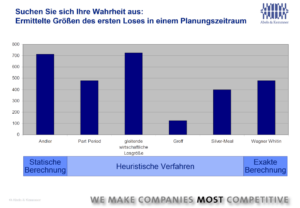
Mitte der 1990er Jahre waren die Computer schnell genug, um auch auf eine große Anzahl an Artikeln das Wagner-Whitin-Verfahren anwenden zu können. In den meisten heutigen Standard ERP-Systemen fehlt es jedoch weiterhin. Dafür werden in den Systemen noch immer die Andlerformel, die für bestimmte Aspekte ihre Berechtigung hat, und die heuristischen Verfahren angeboten. Die Anwender sind damit zufrieden; einerseits wohl, weil sie nicht wissen, dass es bessere Verfahren gibt und andererseits, weil man sich im Laufe der Jahre an alle diese Verfahren gewöhnt hat. Das Wagner-Whitin-Verfahren findet man derzeit zumeist nicht in ERP-Systemen. Es gibt allerdings AddOn-Systeme zur Supply Chain Optimierung, die Wagner-Whitin anbieten. Die sollten Sie sich deshalb anschauen. Wenn Sie dann soweit sind und mit Wagner-Whitin ihre optimalen Losgrößen suchen wollen, dann nun noch ein paar abschließende Hinweise:
Vermeiden Sie falsche kalkulatorische Kosten
Üblicherweise wird bei der Betrachtung der Kosten mit einem kalkulatorischen Wert jeweils für Lagerungskosten und Beschaffungskosten gearbeitet. Für Näherungsberechnungen ist dies hilfreich, bei differenzierterer Betrachtung aber nicht ausreichend. Schauen wir uns dies zuerst einmal am Beispiel der Beschaffungskosten an:
Vielleicht kennen Sie den Fall des Radiergummis, dessen Beschaffung 50 EUR kostet; ein Fall, der vor einigen Jahren durch die Presse geisterte, als man über die Vorteile der Beschaffung über das Internet diskutierte. Wie kommt man in einer Berechnung zu so einem Wert für einen Cent-Artikel? Ganz einfach: Man betrachtet nicht nur den Einkaufspreis des Artikels, sondern berücksichtigt auch die Kosten, die für die Beschaffung des Radiergummis entstehen. Jemand schreibt vielleicht eine Anforderung, diese wird möglicherweise noch vom Vorgesetzten abgezeichnet, dann an den Einkauf weitergeleitet. Evtl. holt der Einkauf für den Radiergummi keine drei Angebote ein.Vielmehr bestellt der Einkäufer via SAP aus einem bereits ausgehandelten Rahmenvertrag den gewünschten Radiergummi. Dazu muss er eine Bestellung anlegen und freigeben. Die Bestellung wird nun noch ausgedruckt, unterschrieben und dann gefaxt. Das Original der Bestellung wird in einem Ordner abgelegt.
Es wird deutlich: Hier entstehen “Beschaffungskosten”,die unabhängig vom Preis der beschafften Ware sehr hoch sein können. In unserem Beispielsunternehmen fallen für den Einkauf im Unternehmen Personalkosten in Höhe von 250.000 EUR an. Der Kostenanteil für die IT-Software und Hardware mögen sich auf weitere 15.000 EUR belaufen. Für die restlichen Kosten fallen nochmals 35.000 EUR an. In Summe “kostet” der Einkauf mit seinen Prozessen im Jahr dann 300.000 EUR. Der Aufwand im Wareneingang beläuft sich auf nochmals 300.000 EUR. In Summe kostet das Bestellen und Vereinnahmen von Waren in unserem Unternehmen also 600.000 EUR. Im Jahr fallen 11.000 Bestellungen an. Hieraus ergibt sich ein Betrag von 54,55 EUR pro Bestellung. So einfach ist die Rechnung – und so falsch ist sie auch!
Was, wenn statt 11.000 Bestellungen im Jahr 15.000 Bestellungen anfallen würden, weil in kleineren Losen bestellt wird? Dann würden bei 240 Arbeitstagen im Einkauf pro Jahr ca. 62 Bestellungen pro Tag ausgelöst statt knapp 46. Die Kosten pro Bestellung lägen dann bei 40 EUR. Die Grenzkosten, d.h. die zusätzlichen Kosten für jede weitere Bestellung lägen bei 0 Euro. Bei der Losgrößenoptimierung, interessieren nur die variablen Bestellkosten, die bei jeder Bestellung neu anfallen. Die fixen Kostenanteile werden erst relevant, wenn sie durch die erhöhte Zahl von Beschaffungsvorgängen steigen.
Selbst bei Kostenpositionen, die vermeintlich wirklich bei jeder Lieferung anfallen, kann dieser Grenzkosteneffekt auftreten. Nehmen wir an,jede Lieferung kostet Frachtkosten in Höhe von 5.Wäre der Radiergummi heute die einzige Bestellung beim Lieferanten, dann wären die 5 den Beschaffungskosten des Radierers hinzuzuzählen. Vermutlich wird aber jeden Tag eine ganze Menge an Büromaterial geliefert. Der Frachtkostenanteil des Radierers beträgt also nur ein Bruchteil der 5. Ob heute ein Teil mehr oder weniger vom Büromateriallieferanten geliefert wird, schlägt sich in den Frachtkosten nicht nieder. Die Grenzkosten sind also Null.
Was zum Schluss bleibt
Je genauer man hinsieht, desto mehr Ungenauigkeiten findet man in der Praxis bei der Berechnung von Losgrößen. Dennoch hat die Losgrößenberechnung ihre Berechtigung. Man muss allerdings die einzelnen Verfahren, geltenden Randbedingungen und Vereinfachungen sehr genau verstehen. Losgrößenoptimierung ist also nicht die einfache Supply Chain Optimierung mittels Formelsätzen, die man einfach im PC berechnen lässt, sondern ein Optimierungsansatz für Spezialisten. Sie setzten die Anwendung der Methode in den richtigen Kontext und stellen die Kostenberechnungen so ein, dass sie genau sind. Alles andere ist ein Stochern im Nebel.
Schlüsselwörter: Losgrössenoptimierung, Supply Chain, Kostenreduktion, Lagerhaltung, Beschaffung
Literatur
[1] Harris, F.W.: How Many Parts to Make at Once Factory: The Magazine of Management 10(2):135-136,152 (1913)