Inventory savings and improved delivery readiness in one
“There is always the wrong product in stock”. Suppliers of immediate and stock programs are particularly familiar with the problem: in order to be able to deliver at all times, the warehouse is filled to the brim and yet the items that the customer needs so urgently are missing.
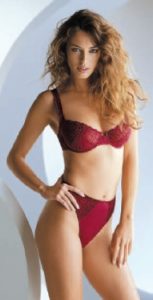
However, the inventories cause high occupancy costs, interest has to be paid on the tied-up capital and, as if that were not enough, the “wrong” inventories can sometimes only be sold at considerable discounts. Production after order placement is not a solution for this type of business. The need to deliver at short notice, usually within 24 to 48 hours, means that it is not possible to order the required materials or manufacture the item to be delivered. In addition, the production costs associated with the small batch size would make the business completely unprofitable.
The many possible variants in the form of styles, fabrics, colors and sizes as well as the lead times of several weeks, even in well-organized companies, lead to this seemingly unsolvable problem. So the stock items are produced to the “best of our knowledge and belief” and a system is sought that combines the best possible combination of low space and capital costs with high delivery readiness and low production costs.
Amazing results
Abels & Kemmner Unternehmensberatung in Herzogenrath has tackled this problem together with the company Anita Dr. Helbig GmbH, a specialist supplier of corsetry and swimwear in Brannenburg: In a careful analysis of stock levels, it was determined that Anita could reduce stock levels by at least 19 percent without compromising its ability to deliver! The starting point was a structuring of article assortments according to sales shares, an attempt to identify trends and seasonalities and a forecast of expected future demand.
Alternative forecasts were carried out with the help of a replenishment optimization tool to determine the effects of changes to the forecasting process, delivery capability, batch size and replenishment time. The result of this logistical fit optimization is astonishing: inventories were reduced by 26 percent and delivery readiness was increased in two stages, first to 94 percent and then to 99 percent.
The detailed project report by Felicitas Heid-Davignon (Anita) and Martin Jürgens (Abels & Kemmner) can be found at www.fashiontechnics.com
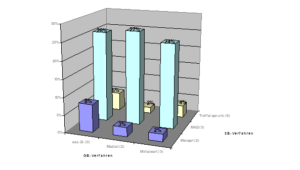