Materialeffizienz
Materialkosten stellen im produzierenden Gewerbe mit ca. 45% den mit Abstand größten Kostenblock dar, noch vor den Personalkosten (18,7%). Grund genug, laufend nach Möglichkeiten zu suchen, die Materialkosten durch effizientere Verwendung des eingesetzten Materials zu senken! Eine richtig gestaltete Wertschöpfungskette und saubere logistische Prozesse können beispielsweise durch Reduzierung von Ausschuss, Bestandsreduzierung, bessere Verbunddisposition, geringeren Verschleiß und geringere Verschrottungsraten ganz wesentlich zur Materialeffizienz beitragen.
Der Blick aus der Perspektive der Materialeffizienz deckt auch ganz neue Möglichkeiten zur Effizienzsteigerung der gesamten Wertschöpfungskette auf.
1% weniger Materialkosten erhöhen die Umsatzrendite um 0,5%.
Mittels Constraint-Analysen legen wir Potenziale zur Verbesserung der Materialeffizienz systematisch offen, identifizieren die wesentlichen Ansatzpunkte zur Verbesserung der Materialeffizienz und entwickeln passgenaue Maßnahmen.
Vielfältige Ansatzpunkte zur Verbesserung der Materialeffizienz
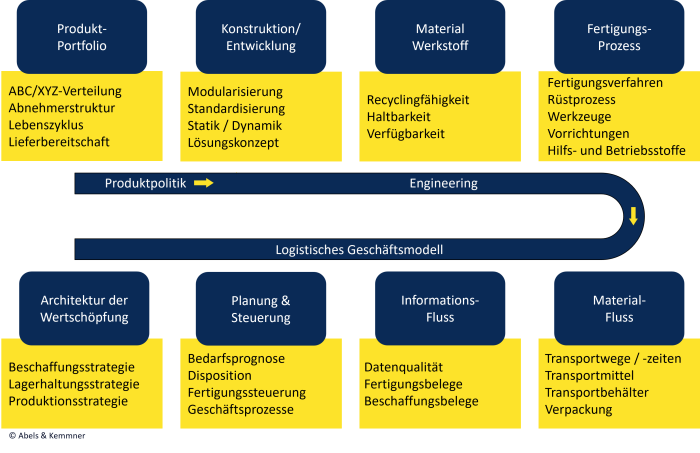
Als Supply Chain Experten betrachten wir unsere einzelnen Leistungen als Bausteine, die sich in das „große Ganze“, einfügen müssen, um das Ziel einer optimierten Supply Chain zu erreichen.
Prof. Dr. Andreas Kemmner